Chain Reactions: Best Risk Management Practices for Ongoing Supply Chain Challenges
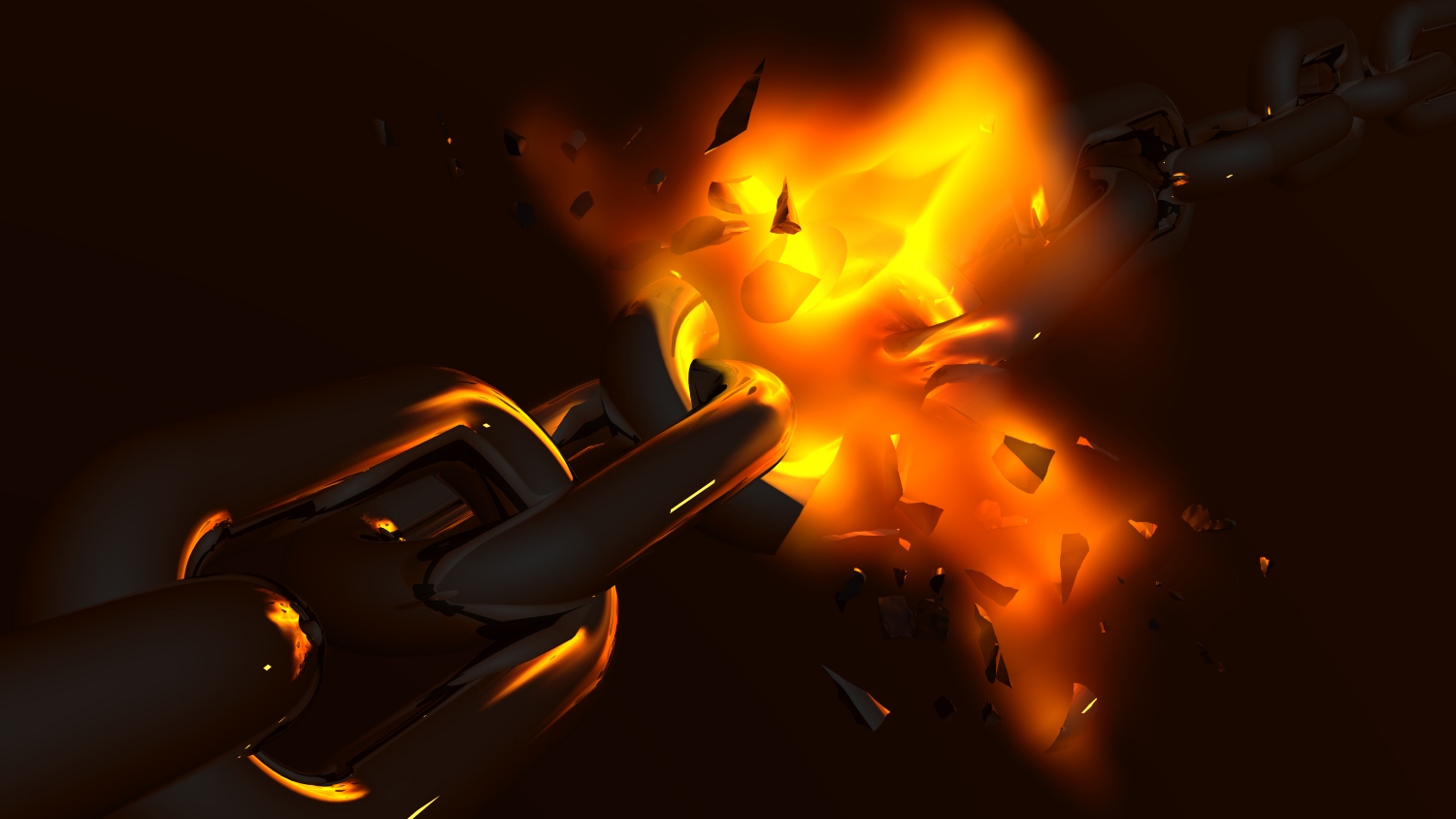
By Samantha Beavers
From semiconductor chip shortages to furniture backlogs, supply chain challenges have been wreaking havoc for more than two years – and they don’t appear to be going anywhere anytime soon. At this stage in the game, most supply chain experts expect these challenges to continue into 2023.
But what’s behind the surge in supply chain issues? How can organizations identify supply chain-related risks on the horizon? And what can they do to manage their risks and come out stronger on the other side?
Rob Handfield, executive director of NC State’s Supply Chain Resource Cooperative, and Ericka Kranitz, director of Poole College of Management’s Master of Management, Risk and Analytics (MRA) concentration, weigh in and provide some context.
Understanding today’s supply chain issues
While organizations have always faced risk in their supply chains, Handfield notes that the overall level of risk has grown significantly in recent years due to increased outsourcing.
“By outsourcing more to low-cost countries, organizations have exposed themselves to a huge amount of risk. Not only are the distances further but the cultures, languages and regulations are also different,” he says.
For a while, most businesses hadn’t given this a lot of thought – but when Covid swept the globe, these risks were impossible to ignore.
“The pandemic really brought to light just how much risk companies were taking,” Kranitz explains. “While organizations were aware of the risks, they were willing to accept them given the productivity gains and because operating cost savings were so valuable. Many believed these risks were being managed and there was a low likelihood that something might happen that would cause the impact we’ve recently seen.”
If the last few years have proved anything, however, it’s that these types of events may be more common than organizations thought. This is why complex global supply chains can be so precarious and potentially devastating.
“Russia’s invasion of Ukraine put additional pressure on supply chains already weakened by Covid, introducing a number of problems. One major one we’re seeing is the shortage of raw materials needed for chip production,” Handfield explains. “Another is food. Because Ukraine is considered the ‘breadbasket of Europe,’ we are already experiencing huge food shortages and price increases, and those are likely to get worse.”
What can be done?
In the face of such challenges, there are a handful of different strategies organizations can consider to minimize their risk and build more resilient supply chains.
One strategy that’s getting a lot of buzz is nearshoring and onshoring. And, in light of national security issues and geopolitical risks, Handfield says, it’s an important one to consider
As an example, Handfield points to his work with the Department of Defense’s COVID-19 Joint Acquisition Task Force (JATF), where he helped identify personal protective equipment (PPE) to protect public health.
“We identified that most health care suppliers were located in East Asia, which means that dependence on foreign suppliers doesn’t only cause disruptions and delays – it can also introduce massive national security risks,” he says. “For this reason, some organizations really need to rethink the design of their supply chains and explore sourcing closer to home.”
However, organizations must realize that this mitigation strategy isn’t simple – and it doesn’t come without problems.
“In our global marketplace, you can’t just flip a switch and bring manufacturing operations back home. If you want to onshore, you really have to put pen to paper to see what it would take to make it happen. What will it cost? How long will it take? Do you have the people to do it? Do you have the materials? What is the impact on the city or region you are moving from? These are all factors you have to consider,” Kranitz explains.
And like other risk management strategies, it can trigger other risks across the organization – which, she explains, is why having an enterprise-wide view of risks is so important.
“Even if you can relocate operations, you have to think about the other risks that you might create by doing so – and the potential impact to your organization’s reputation, profitability, product quality and/or market share,” Kranitz explains. “As with all risks and risk management strategies, organizations have to think about the potential impact on strategic initiatives and take time to plan accordingly.”
And while onshoring might allow companies to eliminate some of the delays caused by bottlenecks at the Ports of Los Angeles and Long Beach, Kranitz notes that it introduces another set of supply chain challenges – including the massive labor shortages and logistics constraints relating to rail and trucking in the United States.
Fortifying the weak links
Because of the various pros and cons involved with nearshoring and onshoring, Handfield and Kranitz recommend that organizations begin by mapping their supply chains – understanding where the most critical materials and services impacting their products and revenue come from.
“Organizations need to map out their supply networks – including their tier one, two and three suppliers – and conduct an analysis to identify the potential risks associated with them. A lot of companies don’t know where their tier two and tier three suppliers are located – but because disruptions can happen on these levels, they need to find this out if they want to understand where they’re most vulnerable,” Handfield explains.
From there, organizations can employ a handful of strategies to strengthen their supply chains – including diversifying their suppliers, looking for low-cost labor in countries with less geopolitical risk and reengineering their products.
“If your suppliers are concentrated in one region but onshoring is not a reasonable solution for you from a cost perspective, then evaluate options to ensure your risks are not heavily concentrated in one or two regions of the world. You don’t necessarily need to bring everything back to the States. If nothing else, you can balance out your portfolio – outsourcing to some suppliers in Europe, some in Asia and so on,” Kranitz explains. “Or, you might find that you can reengineer your products to meet specific specifications and find alternative suppliers.”
“And from that national security standpoint, it is best to try to outsource to countries with democracies and become independent of suppliers located in countries with dictatorships,” Handfield adds.
The bottom line
The best path forward, they agree, is bringing the best minds together to think creatively and come up with long-term solutions – while also keeping an eye on sustainability.
“Rather than tweaking a few things here and there, look hard at what you do and start with a blank canvas. Can you do it differently? Can you do it smarter? And can you make it more cost-effective? And while you’re at it, you might as well start weaving in some better environmental practices and working toward where you want to be in ten years,” she explains.
And when all is said and done, they explain, there’s no magic cure-all for supply chain-related risk – especially for the short-term.
“A lot of what we’re seeing now is beyond our control. It might simply take some time for these issues to work themselves out,” Handfield explains. “However, this should be a lesson to organizations that they have to prepare for these kinds of risks.”
- Categories: